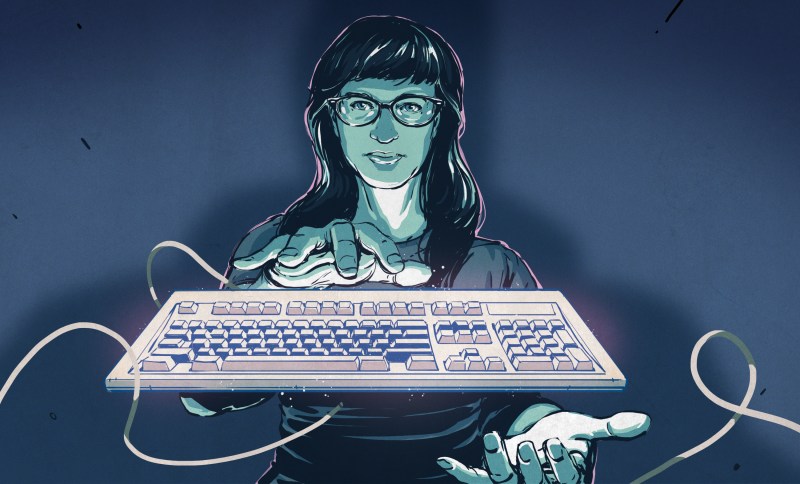
Image by [akavel] via GitHubReader [akavel] was kind enough to notify me about Clawtype, which is a custom wearable chorded keyboard/mouse combo based on the Chordite by [John W. McKown].
First of all, I love the brass rails — they give it that lovely circuit sculpture vibe. This bad boy was written in Rust and currently runs on a SparkFun ProMicro RP2040 board. For the mouse portion of the program, there’s an MPU6050 gyro/accelerometer.
[akavel]’s intent was to pair it with XR glasses, which sounds like a great combination to me. While typing is still a bit slow, [akavel] is improving at a noticeable pace and does some vim coding during hobby time.
In the future, [akavel] plans to try a BLE version, maybe even running off a single AA Ni-MH cell, and probably using an nRF52840. As for the 3D-printed shape, that was designed and printed by [akavel]’s dear friend [Cunfusu], who has made the files available over at Printables. Be sure to check it out in the brief demo video after the break.
Wooden You Like To Use the Typewriter?
Image by [bilbonbigos] via redditI feel a bit late to the party on this one, but that’s okay, I made an nice entrance. The Typewriter is [bilbonbigos]’ lovely distraction-free writing instrument that happens to be primarily constructed of wood. In fact, [bilbonbigos] didn’t use any screws or nails — the whole thing is glued together.
The Typewriter uses a Raspberry Pi 3B+, and [bilbonbigos] is FocusWriter to get real work done on it. it runs off of a 10,000 mAh power bank and uses a 7.9″ Waveshare display.
The 60% mechanical keyboard was supposed to be Bluetooth but turned out not to be when it arrived, so that’s why you might notice a cable sticking out.
The whole thing all closed up is about the size of a ream of A4, and [bilbonbigos] intends to add a shoulder strap in order to make it more portable.
That cool notebook shelf doubles as a mousing surface, which is pretty swell and rounds out the build nicely. Still, there are some things [bilbonbigos] would change — a new Raspi, or a lighter different physical support for the screen, and a cooling system.
The Centerfold: A Keyboard For Your House In Palm Springs
Image by [the_real_jamied] via redditCan’t you feel the space age Palm Springs breezes just looking at this thing? No? Well, at least admit that it looks quite atomic-age with that font and those life-preserver modifier keycaps. This baby would look great on one of those giant Steelcase office desks. Just don’t spill your La Croix on it, or whatever they drink in Palm Springs.
Do you rock a sweet set of peripherals on a screamin’ desk pad? Send me a picture along with your handle and all the gory details, and you could be featured here!
Historical Clackers: the Odell Typewriter
First of all, the machine pictured here is not the true Odell number 1 model, which has a pair of seals’ feet at each end of the base and is referred to as the “Seal-Foot Odell“. Ye olde Seal-Foot was only produced briefly in 1889.
Image via The Antikey Chop
But then inventor Levi Judson Odell completely redesigned the thing into what you see here — model 1b, for which he was awarded a patent in 1890. I particularly like the markings on the base. The nickel-plated, rimless model you see here was not typical; most had gold bases.
These babies cost 1/5th of a standard typewriter, and were quite easy to use to boot. With everything laid out in a line, it was far easier to use a slide mechanism than your ten fingers to select each character. On top of everything else, these machines were small enough to take with you.
No matter their appearance, or whether they typed upper case only or both, Odells were all linear index typewriters. The print element is called a type-rail. There is a fabric roller under the type-rail that applies ink to the characters as they pass. Pinch levers on the sides of the carriage did double duty as the carriage advance mechanism and the escapement.
Round-based Odells went by the wayside in 1906 and were replaced by square-based New American No. 5 models. They functioned the same, but looked quite different.
Finally, John Lennon’s Typewriter Is For Sale
Image via Just Collecting
Got an extra ten grand lying around? You could own an interesting piece of history.
This image comes courtesy of Paul Fraser Collectibles, who are selling this typewriter once owned and used by the legendary Beatle himself. While Lennon composed poems and songs on the machine, it’s unclear whether he secretly wanted to be a paperback writer.
This machine, an SCM (Smith-Corona Marchant) Electra 120, is an interesting one; it’s electric, but the carriage return is still manual. I myself have an SCM Secretarial 300, which looks very much the same, but has a frightening ‘Power Return’ that sends the carriage back toward the right with enough power to shake the floor, depending upon the fortitude of your table.
Apparently Lennon would use the machine when traveling, but gave it to a close friend in the music industry when he upgraded or otherwise no longer needed it. A booking agent named Irwin Pate worked with this friend and obtained the typewriter from him, and Irwin and his wife Clarine held on to it until they sold it to Paul Fraser Collectibles. I find it interesting that this didn’t go to auction at Christie’s — I think it would ultimately go for more, but I’m a writer, not an auction-ologist.
Got a hot tip that has like, anything to do with keyboards? [Help me out by sending in a link or two](mailto:tips@hackaday.com?Subject=[Keebin' with Kristina]). Don’t want all the Hackaday scribes to see it? Feel free to [email me directly](mailto:kristinapanos@hackaday.com?Subject=[Keebin' Fodder]).
From Blog – Hackaday via this RSS feed